Classification of sputtering targets:
Sputtering targets can be categorized into long targets, square targets, round targets and shaped targets according to their shapes.
According to the composition, they can be divided into metal targets, alloy targets, ceramic compound targets.
According to the application field, it can be divided into microelectronic target, magnetic recording target, optical disk target, precious metal target, thin film resistor target, conductive film target, surface modification target, photomask layer target, decorative layer target, electrode target, encapsulation target, and other targets.
According to different applications, they are divided into semiconductor-related ceramic targets, recording medium ceramic targets, display ceramic targets, superconducting ceramic targets and giant magnetic resistance ceramic targets.
Sputtering Targets
Mainly used in the electronics and information industry, such as integrated circuits, information storage, liquid crystal display, laser memory, electronic control devices, etc.; can also be used in the field of glass coating; can also be used in wear-resistant materials, high-temperature corrosion-resistant, high-grade decorative products and other industries.
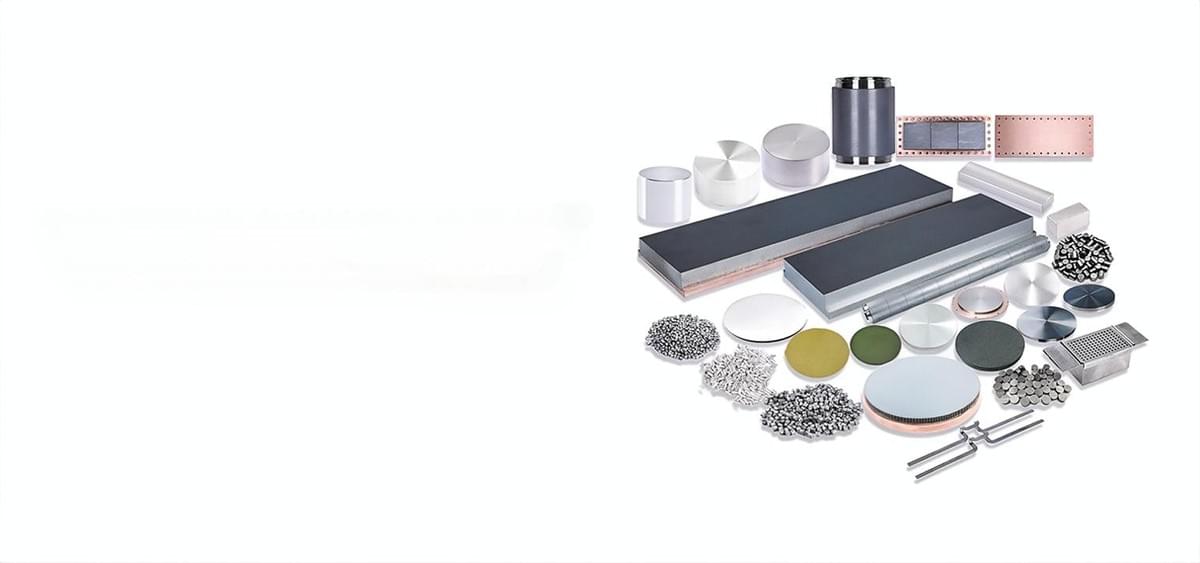
Okay, so I need to figure out what sputtering targets are. Let's start by breaking down the term. "Sputtering" sounds like something related to physics or materials science. Maybe it's a process? And "targets" in this context might refer to objects that are used as a source material in some kind of procedure.
I remember hearing about sputtering in the context of thin film deposition. Maybe sputtering is a method used to deposit thin films onto surfaces. So a sputtering target would be the material that's being deposited. But how exactly does that work?
Sputtering might involve some kind of particle bombardment. Like, using ions to knock atoms off a target material. Those atoms then land on a substrate, forming a thin film. That makes sense. So the target is the source material that gets eroded or "sputtered" away, and the substrate is where the film forms.
What materials are used for sputtering targets? Probably metals, alloys, or ceramics. Depending on the application, different materials would be needed. For example, in semiconductor manufacturing, they might use silicon or other semiconductors. For displays, maybe indium tin oxide for transparent conductive layers.
The process would require high purity materials to ensure the deposited film has the desired properties. Impurities could affect electrical conductivity, optical properties, or structural integrity. So sputtering targets need to be highly pure and maybe have specific microstructures.
How are these targets made? Manufacturing processes might include melting and casting, followed by machining into specific shapes. Or maybe powder metallurgy, where powders are pressed and sintered. The choice of method would depend on the material and the required properties.
Applications of sputtering targets would be in industries that require thin films. Semiconductors for integrated circuits, solar panels for photovoltaic cells, optical coatings for lenses or mirrors, and maybe even decorative coatings. Each application has different requirements, so the targets must be tailored accordingly.
I should also consider the types of sputtering techniques. There's DC magnetron sputtering, RF sputtering, maybe others. Each technique might have different requirements for the target material, like electrical conductivity for DC methods.
Potential challenges in using sputtering targets include target erosion uniformity. If the target wears unevenly, the deposition might become non-uniform over time. Also, maintaining high purity and density in the target material to prevent arcing or defects in the film.
Are there any environmental or safety considerations? Handling materials in sputtering targets, especially if they're toxic or reactive, would require proper safety measures. Recycling of used targets might also be a concern for sustainability.
In summary, sputtering targets are materials used in the sputtering process to deposit thin films on substrates. They need to be high purity, possibly with specific structural properties, and are used in various high-tech industries. The manufacturing process and material choice depend on the application's requirements
Sputtering Targets: An Overview
Definition:
Sputtering targets are specialized materials used in the sputtering process, a physical vapor deposition (PVD) technique. They serve as the source from which atoms are ejected and deposited onto a substrate to form thin films.
Process Mechanism:
Sputtering: High-energy ions (often argon) bombard the target, dislodging atoms due to momentum transfer.
Deposition: Ejected atoms travel through a vacuum and coat a substrate, creating a thin film with specific properties.
Key Characteristics:
High Purity: Essential to ensure film quality (e.g., electrical, optical).
Material Diversity: Metals (Al, Cu), alloys, ceramics (SiO₂, TiO₂), and compounds (indium tin oxide).
Structural Integrity: Dense, homogeneous microstructure to prevent defects.
Manufacturing Methods:
Melting/Casting: For metals/alloys, followed by machining.
Powder Metallurgy: Pressing and sintering powders for ceramics or refractory metals.
Bonding: Attaching targets to backing plates for thermal/electrical conductivity.
Applications:
Semiconductors: Integrated circuits, conductive layers.
Optics: Anti-reflective coatings, mirrors.
Energy: Solar cells, battery electrodes.
Displays: Transparent conductive oxides (e.g., ITO) for touchscreens.
Decorative/Coatings: Wear-resistant or aesthetic finishes.
Sputtering Techniques:
DC Magnetron: Conductive targets, uses magnetic fields to enhance efficiency.
RF Sputtering: For non-conductive materials (e.g., ceramics).
Reactive Sputtering: Introduces gases (e.g., O₂, N₂) to form compound films.
Challenges:
Uniform Erosion: Ensures consistent film quality over time.
Cost: High-purity materials and complex manufacturing raise expenses.
Thermal Management: Heat generation during sputtering requires cooling systems.
Environmental/Safety Considerations:
Toxic Materials: Handling precautions for targets like cadmium or lead.
Recycling: Reclaiming precious metals (e.g., Au, Ag) from used targets.
Conclusion:
Sputtering targets are critical in advanced manufacturing, enabling precise thin-film deposition across industries. Their design and production are tailored to meet stringent performance criteria, driving innovation in technology and materials science.
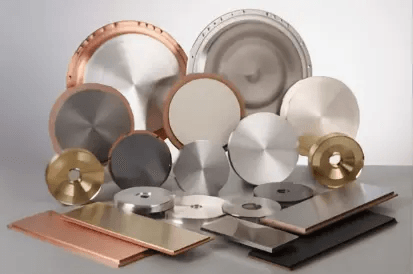
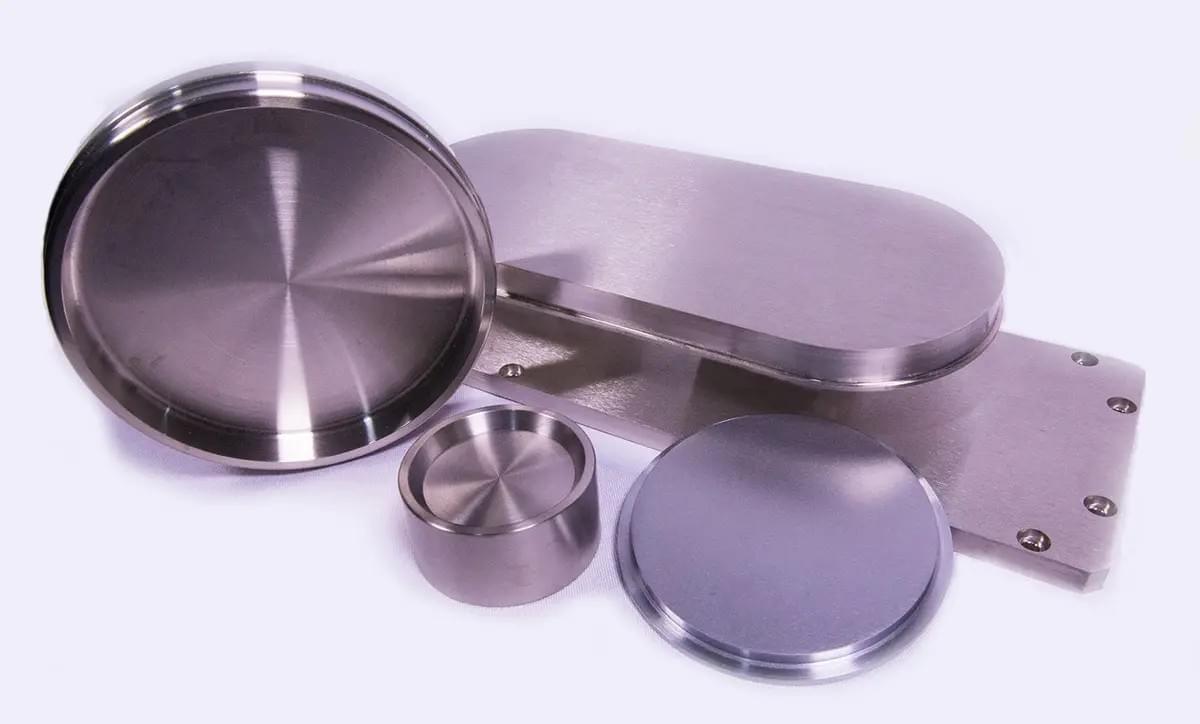