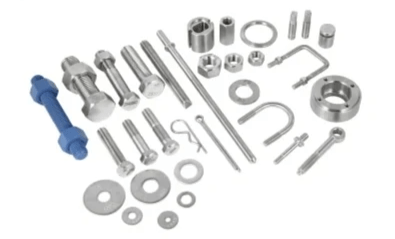
Artisan industry, professional Nickle alloy / superalloy fasteners factory.
We can produce Bolt , Nut, Washer, Threaded rod, Split cotter Pins, R clips and machining special parts according to the drawing with material of Hastelloy,Monel,Incoloy,Inconel,Titanium , Duplex series,Nimonic and normal stainless steel.
Inconel superalloys Fasteners
Artisan industry specialized in superalloy Fasteners Bolt & Nut Manufacturing , also produce precision superalloys components(high performance, superalloys parts for critical applications). These include Nickel alloys which are often referred to as the Inconel, Incoloy, Monel and Hastelloy.
Inconel alloys were first developed by Wiggin Alloys in Hereford (West Midlands, England) during the 1940’s before they were eventually acquired by the Special metals Corporation.
Nickel alloys are commonly used within high temperature applications and highly corrosive environments or a combination of the two. It is also well suited for environments where by it may be subject to high pressure and temperature. Therefore it is found commonly within turbine blades, pressure vessels and heat exchanges.
Hexagon bolts, Setscrews, Plugs, Capscrews and Nuts defined to BS, ANSI, ISO, DIN & NFE can be machined to order within 24 hours if required.
The most common grades are as follows:
Nickel Grades
UNS N06600 Alloy 600 Inconel 600
UNS N06601 Alloy 601 Inconel 601
UNS N06625 Alloy 625 Inconel 625
UNS N07718 Alloy 718 Inconel 718
UNS N07718 AMS 5663 (B637 N07718)
From the above grades, we have manufactured components including; Hex bots, Hex Nuts, Taper Pins, T bolts, Self locking nuts, Keys, Engineers studs, stud bolts, washer and various other machined components.factory can also perform upgrade heat treatment and chemical and mechanical testing to ASME, b637, AMS 5663 and API 6A as well as other customer specific material procedures and process specifications.
Inconel is an austenitic nickel-chromium based superalloy. It was developed by Wiggin Alloys in the 1940s for use in the Whittle engine, and is a brand name commonly used to refer to the class of alloys.
Like all other superalloys, Inconel is used for high temperature applications that require high creep resistance.
Inconel families include 600, 617, 625, 690, 718, and X-750 alloys along with other less common variations. A unique property of Inconel is the creation of a thick oxide layer that is formed when it is heated that protects the rest of the material from oxidative or corrosive damage. Unlike other superalloys that rely on single crystal casting to control creep, it uses crystal vacancies in its structure to avoid the creation of a grain that will allow creep to occur.
Like other superalloys, some Inconel alloys use solid solution strengthening to insert atoms of the alloying metal into the crystalline structure of the base material. Other Inconel alloys use precipitation hardening to insert impure particles into the material’s crystalline structure. This causes the yield strength anomaly to occur and the yield strength of the material stays constant over most of its operating temperature. In these alloys, a small amount of niobium is added to the nickel compound to form small crystals that reduce slip and creep.
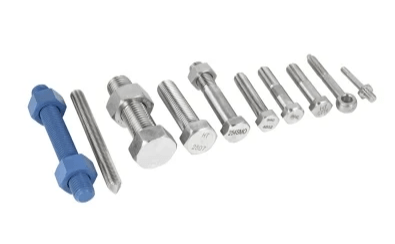
Inconel Bolts
Inconel parts are extremely hard to machine because work hardening will cause the tool to deform after the first pass. Welding of most of these alloys causes damage due to local crystallization changes due to the heat produced. Some alloys such as 625 and 718 are formulated specifically to allow welding.
Applications
Aerospace
Inconel is commonly used in the aerospace industry due to its excellent high temperature mechanical properties. The space shuttle program used eight Inconel studs to attach the entire space shuttle to the launch platform. The total weight of the system held by the 8 studs was 4.465 million pounds.
North American Aviation created a rocket powered aircraft for the United States Airforce that qualified 8 pilots as astronauts because the plane was technically able to fly in space and set the record for the highest speed ever reached by a manned aircraft in 1967 at mach 6.7. Because of the extreme the aircraft was subjected to during its flight, a skin made of Inconel X.
Inconel X-750 was used in the engine manifold of the Saturn V. It is currently used for the Merlin engine used to power the SpaceX Falcon 9. SpaceX was also able to 3D print a rocket engine with a combustion chamber made of Inconel.
Inconel is also engraved to record flight information in airplane black boxes.
Automotive
Inconel is an excellent choice for use in automotive applications, especially turbocharger systems and exhaust systems, due to it’s performance at high temperatures and pressures. The most notable use is in NHRA Top Fuel and funny cars. The exhaust valves of both cars are made from Inconel 751.
BMW uses Inconel exhaust manifolds in their high-performance M series cars, including the M5 E34. Jaguar also uses an Inconel Titanium alloy for the exhaust system on the F-Type series. Formula One, NASCAR, and APR also use Inconel for the exhaust systems of their racecars.
Ford uses Inconel to create the turbocharger turbines for the EcoBlue diesel engines. Norton Motorcycles also use Inconel in their exhaust systems to handle the 1,000°C operating temperature.
Tesla upgraded from steel to Inconel for the main battery contactor on the Model S to allow higher flexibility at higher electrical loads. This allows a safe 1500-amp output to be used and enables “Ludicrous Mode”.
Other Uses
High quality suppressors use Inconel baffle stacks to handle the extreme heat and pressure created when firing a machine gun. The manufacturers are so confident in the material, they usually offer lifetime warranties.
Inconel 718 is commonly used to make cryogenic tanks and wellhead parts.
Inconel 690 was developed with a low cobalt content and high chromium content to be used in nuclear applications. This alloy is used for piping, separators, and weldments in nuclear plants. The alloy is also used for heat treating equipment.
Inconel X-750, 751, and 792 are used to make components in gas turbine systems and is chosen for the high temperature mechanical properties and chemical resistance required.
Inconel stud Bolt
1. Standard: DIN975/976
2. Grade: Inconel 690 , 2.4662 , UNS N06690
3. Material: Inconel 690 , 2.4662 ,UNS N06690
4. Colour: Bright
5. Package: Bulk in 25 kg carton, then in pallet
6. Delivery time: 45days
Inconel series | Inconel600/601/617/690/625/718/X750 |
Advantages | Good price, Fast service , MOQ:10 PCS |
Iinconel 690 has outstanding resistance to oxidizing chemicals and to high-temperature oxidizing gases. And it has resistance to stress corrosion cracking in chloride-containing environments as well as to sodium hydroxide solutions.
nickel inconel 690 is used for applications such as coal-gasification units, burners and ducts for processing sulfuric acid, furnaces for petrochemical processing, incinerators and so on.