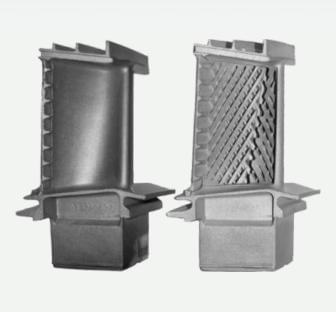
Lost wax vacuum casting precision casting superalloy turbine blade and guide vane used for turbojet
Inconel 625、Inconel 718、AISI 316、Monel
Lost wax vacuum casting precision casting superalloy turbine blade and guide vane used for turbojet engine and turbocharger manufacturing(Aero engine, gas turbine parts)
Superalloy turbine blade and guide vane used for turbojet engine, turbine blade and guide vane be finished by integral casting. And casting method of turbine blade and guide vane is lost wax investment & vacuum casting, casting surface smoothness can meet Ra3.2μm, production process of turbine blade and guide vane is Silica sol process. The material of turbine blade and guide vane is Inconel713c.
The rotating speed of impeller is 18000RPM, overspeed is 20700RPM.The dynamic balancing accuracy is G1.
What are the advantages of integral casting instead of welding process:
* The overall consistency of the impeller is good
* The dynamic balance is good
* Production cost is lower
All impeller will be done X-Ray inspection and fluorescent penetration test in our factory, including CMM, tensile strength test and hardness test.
Our main products: compressor housing, compressor cover, compressor shell, multistage compressor impeller, single stage compressor impeller, open compressor impeller and closed compressor impeller, fluid machinery multistage compressor impeller, compressor impeller, centrifugal compressor impeller,Magnetic suspension blower impeller, air suspension blower impeller, compressor impeller, multistage comprssor impeller, fan impeller, blower impeller, fan blade, blower cooling flow, blower diffuser, blower housing. ...
casting process is precision vacuum investment casting.
All inspection process will be finished in our factory, including non-destructive inspection and destructive inspection
Non-destructiove inspection: *Visual inspection *Surface defect testing *Dye penetrant testing * Radiography testing * Ultrasonic testing *Size testing by CMM
Destructiveinspection: *Tensile strength testing *Yield strength testing *Hardness testing *Chemical composition testing by spectrograph
Non-destructive Testing
1. Visual Inspection
2. Surface Defect testing----- FPT Fluorescent Penetrant Testing
3. Inside Defecting Testing---- Radiography Testing / Ultrasonic Testing
4. Size Testing-----Germany ZEISS CMM /3D Scanner
Destructive Testing
1.Tensile Strength Test----- Room/High Temperature Tensile Testing Machine
2.Creep Strength Test-----Creep Tensile Testing Machine
3.Hardness Testing------ Rockwell Hardness Tester
4.Surface Grain Size Testing-----Metallography Testing
5.Chemical Composition ------Germany SPETRO Spectorgraph
What is Nickel-based alloy Castings?
Nickel-Based Alloys for Investment Casting
Alloy choice is a very important aspect of part design. Choosing the right nickel-based alloy is dependent on several factors, including the environment
the nickel based castings will be exposed to while in service. Furthermore, if the nickel based alloy castings are going to be used in conjunction with a wrought component (i.e.welding two components together) it is important to have a preliminary discussion withour metallurgist to ensure you choose the appropriate chemistry and matericl properties suitable for your application.
● Nickel-based alloys are known for their oxidation and corrosion resistant properties in harsh environments and high-temperature applications.
● Hast alloy is a nickel based metal casting alloy, and it is highly resistant to corrosion.The inclusion of molybdenum makes Hast alloy harder,stronger at high temperatures, and makes it great for welding applications.These nickel based alloy castings are easily fabricated and formed.They have good ductility and can be forged and cold worked.
Here are some of the most commonly used nickel-based alloys
K418、K418B 、Inconel713C、 Inconel713LC 、Hast alloy C276 、DIN/EN 2.4819
What is Cobalt-based alloy Castings?
Cobalt is a hard,lustrous,silver-gray metal that is naturally protected against oxidization (rust) by a passivating oxide film.Like nickel,cobalt can only be found in nature in chemically combined forms (natural alloys); pure cobalt can be produced via reductive smelting.
Cobalt alloys are corrosion-resistant,heat-resistant,and wear-resistant.This makes cobalt-based alloy castings useful in numerous industries, including medical, aerospace, automotive, military,andother applications where oxidization is problematic and high strength is critical. In the medical industry, for
example,cobalt-based investment castings are used to create orthopedic implants that do not wear down over time. Cobalt alloys are used in high friction bearing environments for their strength and lubricity (or anti-galling quality).In high-temperature environments,such as turbocharger turbines and jet aircraft turbines, cobalt alloys exhibit good creep resistance,as well as resistaince to thermal fatigue.